kasuriかすりとはどんなもの?
Kurume kasuri is a type of kasuri that is kind of kimono that has been produced in the Chikugo region in the southern part of Fukuoka prefecture.
This area has prospered as a castle town for a long time., and around Around 1800, Den Inoue,at the age of 12, (12 years old at that time), who was in the former Kurume Domain, proposed the origin of created Kurume Kasuri.
Kurume kasuri It is characterized by its white pattern.
To create the pattern, a bundle of threads is first tied (kasuri kukuri) and then dyed.
At this time, The tied (tied) part remains white without being dyed, so this part emerges as a pattern.
Then, by weaving the dyed threads one by one, a single piece of fabric is created.
Superior techniques honed by human hands and time, such as lead its complicated patterns.
Kurume kasuri is made by combining the warp and weft threads to create a single kasuri Kasuri pattern.
In addition, By wrapping the bundles of warp threads with a hemp skin called ramie, it is becomes possible to quickly and accurately emboss a wide variety of patterns quickly and accurately according to the pilot’s leading thread called Eito.
, the complicated kasuri pattern is woven. In 1957, Kurume Kasuri became the first cotton fabric to be designated as an Important Intangible Cultural Property of Japan in 1957.
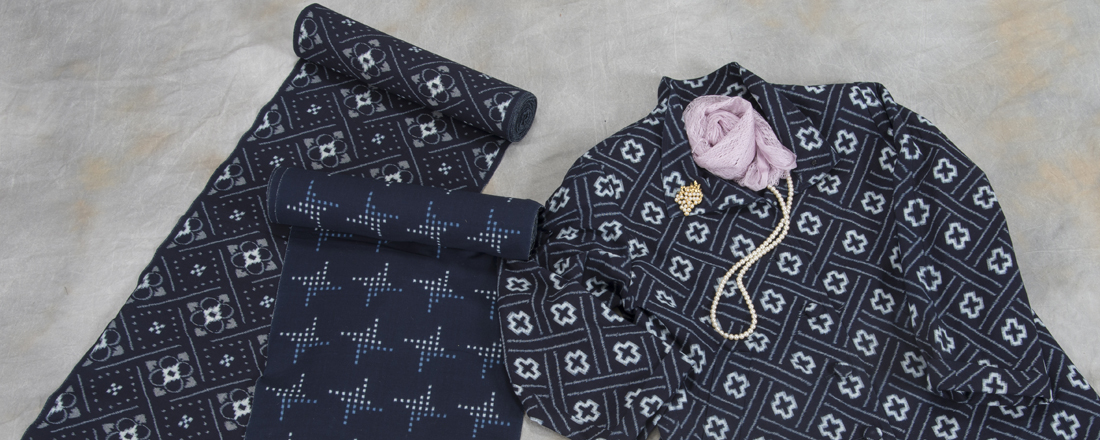
charm久留米絣の魅力
Kasuri is also written as flying white. The white that is left undyed here and there in the navy blue is flying out and it is a good representation of the pattern.
Hazel, it’s a hazy beauty.
When the dyed threads are undyed by tying them at regular intervals, the center of the tying part is left white and the ends are mixed with the dyed color and white.
If you weave these threads in warp, weft, or warp and weft combinations, the undyed white area will be distorted. This part is called kasuriashi, and it can be said that kasuri weaving finds a simple beauty in the pattern in this faint part.
history歴史
Kurume Kasuri is said to have originated around 1800 when Den Inoue (12 years old at the time), who was in the former Kurume Domain, came up with the idea. One day, Chun noticed white spots on her clothes that had faded from being submerged in water several times.
Enchanted by the rough beauty of the specks, Den can’t stop her inquisitive mind from boiling over.
She hurriedly unwrapped her clothes and followed the black and white of her threads and tied them.
Then, I dyed it with indigo juice, dried it, and threaded the tying thread.
– What do you think? When I put this on, hundreds of white spots appeared on the surface of the fabric, creating a new fabric with a mysterious charm. This fabric was named “Kasuri” because it looks faded in places.
This is the beginning of Kurume Kasuri.
Artistry as an important intangible cultural property.
Diverse facial expressions.
And the familiar warmth that is always next to people.
For those who love Kasuri, the name Inoue Den cannot be forgotten.
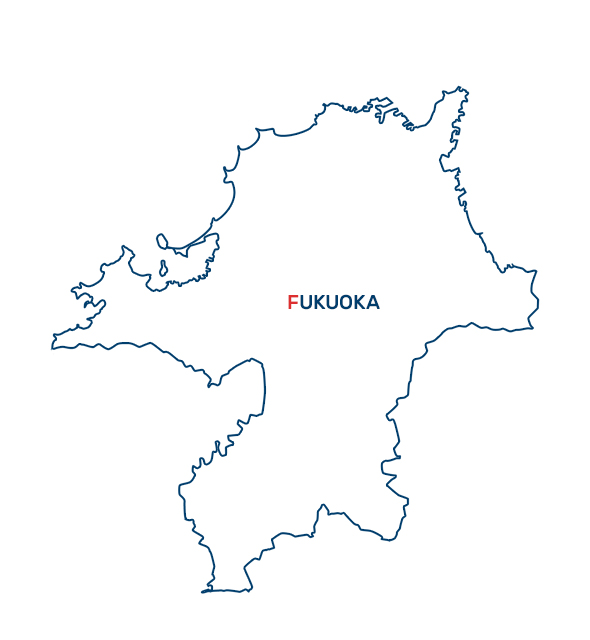
production area産地
India is said to be the home of Kasuri.
It was introduced to Okinawa around the 14th century from India through the southern islands of Borneo and Sumatra.
In Okinawa, things around us, such as clouds, water, swallows, and regulations for carpenters, were simply and concisely designed and woven into kasuri.
Ryukyu Kasuri.
Kurume Kasuri is a unique Japanese Kasuri that was devised by Den Inoue in Kurume at the end of the 18th century.
features特徴
- 100% cotton and gentle on the skin
- Wearing it alone in the summer will keep you cool, and in the winter, it will keep you warm when you wear it in layers. (Wearing season is long)
- Easy to clean and can be washed at home.
- The more you wear it, the more softness and texture unique to cotton fabric will come out.
- Designed with ease of movement and a beautiful silhouette, you can use it for many years without getting tired of it.
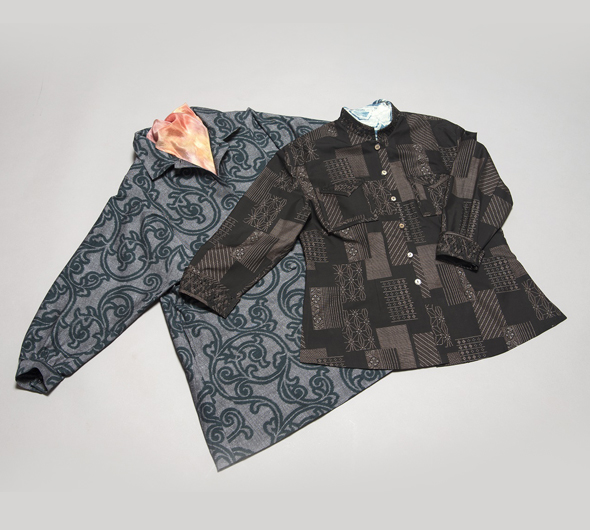
お手入れ方法は簡単
01 | Add an appropriate amount of dry detergent that can be used at home to the water and press it to wash. |
---|---|
02 | After that, soak it for 10-15 minutes and rinse it once or twice under running water. |
03 | Remove from water and squeeze lightly. If you use a dehydrator, take it out early and do not overspray. After dehydration, stretch the texture of the ground. |
04 | Turn it inside out to arrange the mold and dry it in the shade. At that time, if you try to smooth out the wrinkles, you don’t need to iron it after it dries. |
- ※It is a good idea to wash the dirt as soon as possible. Also, if you do not avoid dust, you will get dusty. Indigo dyeing is especially easy to burn, so please be careful.
- ※Clothes using Ojiya Chijimi are hemp fabrics, but they can be washed by hand just like cotton.
- ※Clothes made from Oshima Tsumugi are silk fabrics, so we recommend that you take them to the dry cleaners.
Production製作工程
-
- 01.Pattern making (design), drawing paper
First, we design the Kasuri pattern.
The design is drawn on special paper such as graph paper, and the distribution and placement of the threads is determined.
-
- 02.Making a warp ruler
Make a sutra scale according to the picture paper.
-
- 03.Rough drawing
Drawing of thread Considering the contraction of the weft, rewrite the design.
Eitokaki is the process of creating the threads that form the basis for binding the weft threads.
The tightly stretched white threads are carefully marked with ink according to the rough sketch.
-
- 04.Warp fly (warp adjustment), weft fly (wet adjustment)
Once the kasuri yarn distribution is determined, the warp and weft yarns necessary for weaving are prepared.
-
- 05.Threading (scouring), bleaching (bleaching), sizing
It is boiled for 2-4 hours to remove impurities from the threads.
By bleaching and sizing, the threads are prevented from becoming untidy and fuzzy, then dry.
-
- 06.Hand-tied
It is a work to resist dyeing by tying the part that will be the pattern of the warp and weft.
The tied part will not be colored when dyeing, and the untied part will become the pattern.
This is the origin of the kasuri pattern, and it is an important process that affects the finish of the work.
-
- 07.Indigo dyeing, indigo dyeing, washing
Preparations for dyeing with indigo (indigo dyeing) are performed, and the threads are dyed.
For indigo dyeing, the thread is beaten and air is added 15 to 20 times to improve the dyeing.
Soak in warm water overnight to remove impurities, excess dye, and scum from the threads during indigo dyeing.
-
- 08.Indigo solution
Stretch the washed thread and quickly untie the coarse ramie before it dries.
-
- 09.Washing, bleaching, sizing, drying
Wash and bleach again to bring out the dyed colors.
Starching prevents fluffing of the threads, increases strength, equalizes the tension of the warp threads, prevents the kasuri and threads from being disturbed, and facilitates weaving. and dry in the sun.
-
- 10.Warp split (pattern matching)
When binding, the threads are folded in four, so they are split and stretched out, and the warp threads are bundled to form a pattern.
-
- 11.Interrupting and sleying
Plain threads and Kasuri are arranged according to the number of threads decided on the drawing paper.
The lined up warp threads are passed through the reed blades in order from the end.
-
- 12.Warp winding
The warp is wound on the winding box to set the warp on the loom.
-
- 13.Azekake (Heddle Threading), Weft Splitting, Weft Splitting, Frame Raising, Kanmaki)
-
- 14.Handwoven
In the case of hand weaving, a throwing shuttle is used to carefully weave the fabric while matching the patterns.
It requires experience and skill.
-
- 15.Hot water and drying
The paste applied during the process is removed and the texture is improved.
-
- 16.Straightening, inspection, completion of Kurume Kasuri
Place the woven fabric on the shakudai, remove the stitches with scissors, and cut to the specified length while checking the width and finish.
Fold it in four and roll it.
This completes the Kurume Kasuri.
- Home
- About Kurume Kasuri